1. Stepper signal interface
The stepper signal interface of the stepper motor driver mainly receives the pulse signal sent by the controller and controls the motor to rotate according to a certain number of steps. It includes pulse signal, direction signal and enable signal. The pulse signal is the main signal to control the rotation of the motor, the direction signal is used to control the forward and reverse rotation of the motor, and the enable signal is used to control the motor to enable or disable. It should be noted that the pin number of each interface may be different, and it must be wired according to the actual interface.
2. Power interface
The power interface of the stepper motor driver is the main interface for receiving power input. It is necessary to pay attention to the voltage, current and other parameters of the interface. When wiring, the polarity of the power supply should be confirmed to avoid burning the driver due to wrong connection.
3. Control interface
The control interface of the stepper motor driver receives the command sent by the controller to control the movement of the motor. The control interface generally includes serial port, parallel port, network interface, etc., which needs to be selected according to the actual use environment.
4. Protection interface
The protection interface of the stepper motor driver generally includes protection mechanisms such as overcurrent protection and overvoltage protection. When the working current or voltage of the motor exceeds the preset value, the protection interface will automatically stop the motor to avoid damage to the entire circuit. Therefore, the protection interface is a very important part of the stepper motor driver.
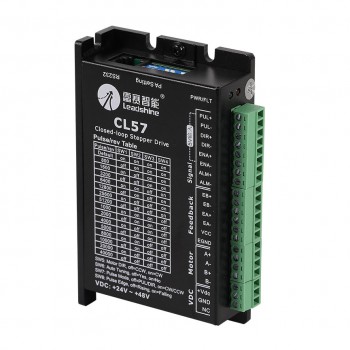
5. Other interfaces
In addition to the above 4 main interfaces, the stepper motor driver has some other interfaces, such as limit interface, encoder interface, etc. The limit interface can be used to control the stroke of the motor. When the motor turns to the preset position, it will trigger the limit switch to stop the motor movement. The encoder interface can be used to feedback the state of the motor movement in real time, so as to control the motor movement more accurately.
In short, each interface of the stepper motor driver plays an important role and is crucial. Therefore, when using the stepper motor driver, it is necessary to carefully understand the role and use of each interface, and perform correct wiring operations according to the actual situation to ensure the safe and stable operation of the motor.